Elektrifiering och automatisering har utvecklats snabbt i Kina.Molded-case circuit breakers (MCCB) har använts i stor utsträckning för sina bra överbelastnings- och kortslutningsskyddsfunktioner.
1.Bakgrund:
Elektrifiering och automatisering har utvecklats snabbt i Kina.Molded-case circuit breakers (MCCB) har använts i stor utsträckning för sina bra överbelastnings- och kortslutningsskyddsfunktioner. MCCB, som de mest grundläggande skyddsapparaterna, har omfattande tillämpning, ett brett utbud av sorter och kompakt och komplicerad struktur. Tidigare fann designers och tillverkare av elektriska apparater ofta det nödvändigt att tillverka prototypdelar genom silikonbeläggningsbearbetning och CNC-bearbetning och att utföra verifiering och testning i design- och utvecklingsstadiet av nya produkter, vilket skulle kräva en lång bearbetningscykel och höga kostnader och bli ett stort problem om dussintals eller hundratals nya produkter behövde utvecklas varje år. Nedan presenteras ett ärende med en slutkund av TPM3D.
2.Kundprofil:
Kunden är en världsberömd leverantör av smarta energilösningar, och dess produkter inkluderar kraftdistributörer, terminalapparater, motorstyrning och skyddsapparater, industriell automation etc. Med en årlig försäljning på över 80 miljarder RMB är företaget verksamt i mer än 140 länder och regioner. Denna kund kombinerar TPM3D P360 lasersintringssystem med PPS för sin FoU och provproduktion av olika lågspänningsapparater.
3.Produktutveckling:
Kunden utvecklar och producerar mer än 10 000 nya elektriska produkter varje år. För närvarande inkluderar dess huvudprodukter tryckta med TPM3D P360 fodral för gjutna brytare och andra konstruktionsdelar.
Efter att provet har skrivits ut kommer kunden att genomföra monteringsverifiering och funktionstester. Noggrannheten i monteringsverifieringen krävs för att nå ±0,2 mm. Funktionstesterna inkluderar huvudsakligen: hållfasthetstest, långt fördröjningstest, isoleringstest etc. Materialet som antas är 30% glasplädförstärkt nylon 12 (Precimid1172Pro GF30) av TMP3D, som har utmärkt styrka och slaghållfasthet. Enligt kunden kan materialen uppfylla testkraven när det gäller mekaniska egenskaper och isolering. Dessutom når materialets termiska deformationstemperatur så högt som 184,4 ° C, och de tryckta fodralen kan testas utan att deformeras i en termostat vid 80 ° C i 4 timmar, vilket uppfyller kraven i det långa fördröjningstestet. På det hela taget är fall av gjutna brytare tryckta med SLS-teknik i nivå med traditionella formsprutade delar.
4.Miljövänligt:
Vid köp av lasersintringssystemet P360 konfigurerade kunden också en Parts & Powder Processing Station (PPS), som lanserades 2018 av TPM3D, den första i Asien, integrerar delrengöring, pulveråtervinning, blandning, matning och pulveruppsamling, löste problemen som tidsslöseri, föroreningar och säkerhet vid arbetsdrift. PPS har passerat den nationella standarden för dammexplosionssäker zon 22 och den internationella CE-certifieringen och fått högt erkännande för sin bättre prestanda för att säkerställa användarsäkerhet.
5.Kostnadsminskning och effektivitetsförbättring:
Innan SLS 3D-utskriftssystem introducerades antog kunden CNC-bearbetning eller outsourcad silikonbeläggningsbearbetning, vilket tog minst 5-6 dagar att erhålla testdelarna. Efter att lasersintringssystemet P360 sattes i produktion kunde prover erhållas och testas efter bara 48 timmar, vilket sparar tid med mer än 60%. Tidigare kostade outsourcad ärendehantering cirka 4 000 RMB / set. Med SLS 3D-utskriftsteknik kan kostnaden styras under RMB 700/set, en minskning med mer än 80%. Med en hög utnyttjandegrad kan kundens utrustning för närvarande skriva ut 2-3 hela kammaren per vecka i genomsnitt. Dessutom kan det enligt kunden spara cirka 700 000 RMB per år, vilket bättre minskar kostnaderna och förbättrar effektiviteten.
Jämförelse av kostnad och cykel mellan traditionell process och SLS 3D-utskriftsprocess:
"TPM3D: s P360-system är bekvämt och snabbt; PPS minskar manuell intervention samtidigt som man uppnår hög bearbetningseffektivitet för delar och pulver. Lösningen sparar tid och kostnader och säkerställer en snygg och säkrare miljö."
——Feedback från kunden
Elektrifiering och automatisering har utvecklats snabbt i Kina.Molded-case circuit breakers (MCCB) har använts i stor utsträckning för sina bra överbelastnings- och kortslutningsskyddsfunktioner. MCCB, som de mest grundläggande skyddsapparaterna, har omfattande tillämpning, ett brett utbud av sorter och kompakt och komplicerad struktur. Tidigare fann designers och tillverkare av elektriska apparater ofta det nödvändigt att tillverka prototypdelar genom silikonbeläggningsbearbetning och CNC-bearbetning och att utföra verifiering och testning i design- och utvecklingsstadiet av nya produkter, vilket skulle kräva en lång bearbetningscykel och höga kostnader och bli ett stort problem om dussintals eller hundratals nya produkter behövde utvecklas varje år. Nedan presenteras ett ärende med en slutkund av TPM3D.
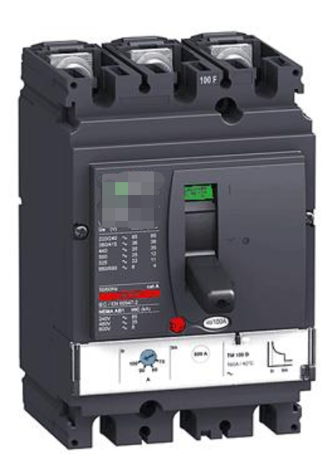
En typ av gjuten brytare
2.Kundprofil:
Kunden är en världsberömd leverantör av smarta energilösningar, och dess produkter inkluderar kraftdistributörer, terminalapparater, motorstyrning och skyddsapparater, industriell automation etc. Med en årlig försäljning på över 80 miljarder RMB är företaget verksamt i mer än 140 länder och regioner. Denna kund kombinerar TPM3D P360 lasersintringssystem med PPS för sin FoU och provproduktion av olika lågspänningsapparater.
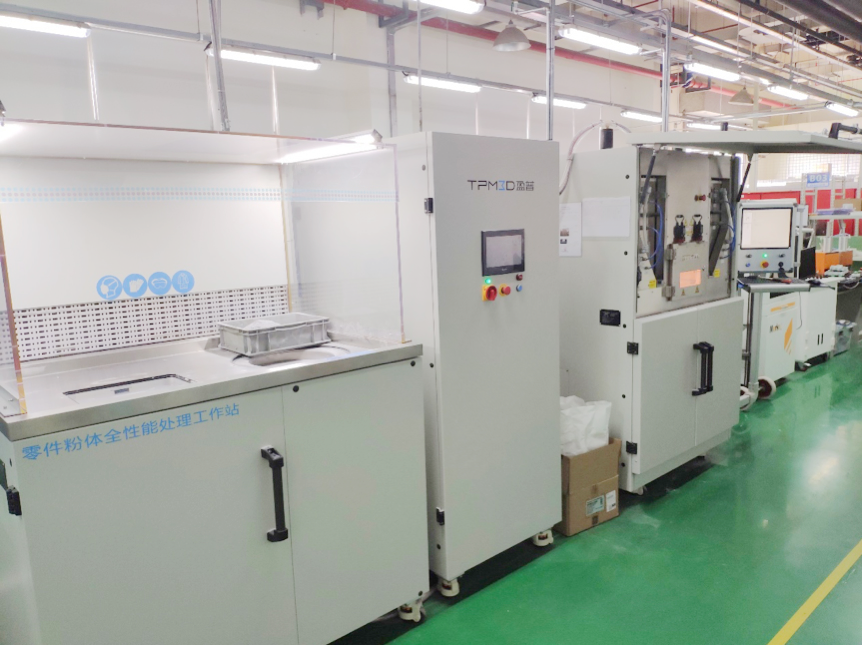
TPM3D P360 Lasersintringssystem + PPS
3.Produktutveckling:
Kunden utvecklar och producerar mer än 10 000 nya elektriska produkter varje år. För närvarande inkluderar dess huvudprodukter tryckta med TPM3D P360 fodral för gjutna brytare och andra konstruktionsdelar.
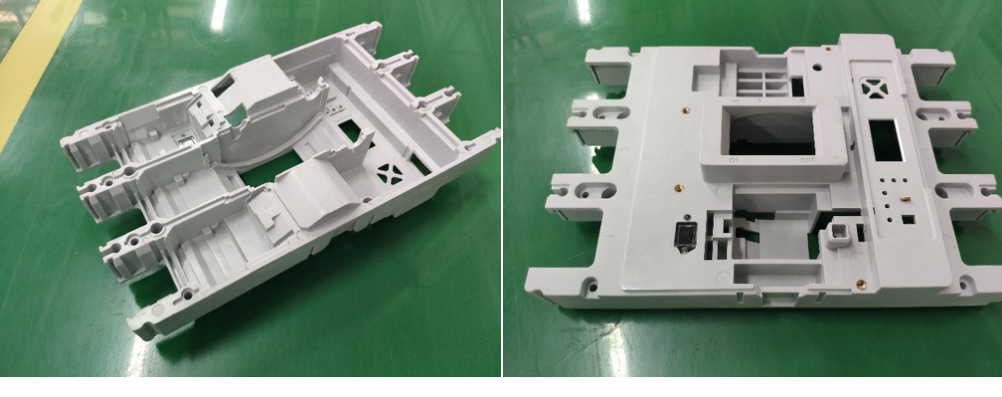
gjuten brytare utvecklad av SLS-teknik
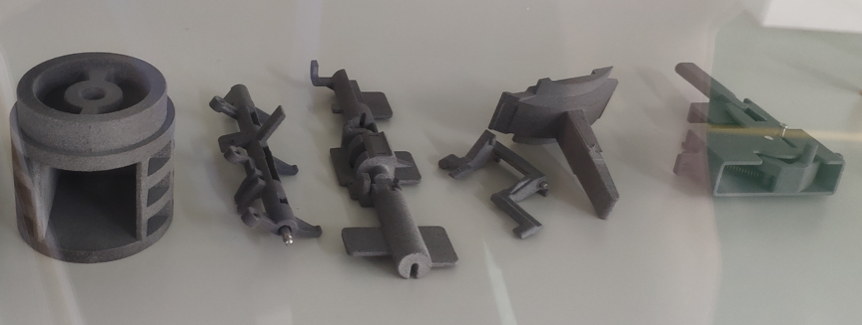
Andra konstruktionsdelar
Efter att provet har skrivits ut kommer kunden att genomföra monteringsverifiering och funktionstester. Noggrannheten i monteringsverifieringen krävs för att nå ±0,2 mm. Funktionstesterna inkluderar huvudsakligen: hållfasthetstest, långt fördröjningstest, isoleringstest etc. Materialet som antas är 30% glasplädförstärkt nylon 12 (Precimid1172Pro GF30) av TMP3D, som har utmärkt styrka och slaghållfasthet. Enligt kunden kan materialen uppfylla testkraven när det gäller mekaniska egenskaper och isolering. Dessutom når materialets termiska deformationstemperatur så högt som 184,4 ° C, och de tryckta fodralen kan testas utan att deformeras i en termostat vid 80 ° C i 4 timmar, vilket uppfyller kraven i det långa fördröjningstestet. På det hela taget är fall av gjutna brytare tryckta med SLS-teknik i nivå med traditionella formsprutade delar.
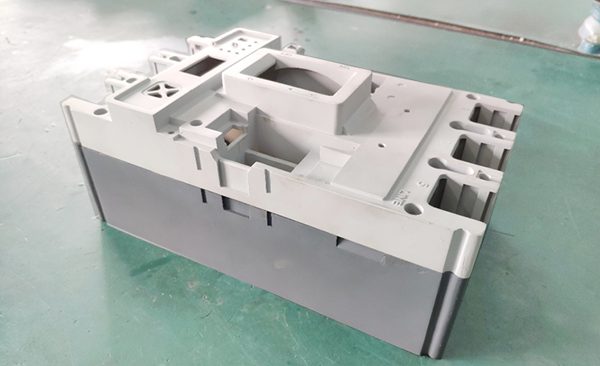
Verifiering av montering
4.Miljövänligt:
Vid köp av lasersintringssystemet P360 konfigurerade kunden också en Parts & Powder Processing Station (PPS), som lanserades 2018 av TPM3D, den första i Asien, integrerar delrengöring, pulveråtervinning, blandning, matning och pulveruppsamling, löste problemen som tidsslöseri, föroreningar och säkerhet vid arbetsdrift. PPS har passerat den nationella standarden för dammexplosionssäker zon 22 och den internationella CE-certifieringen och fått högt erkännande för sin bättre prestanda för att säkerställa användarsäkerhet.
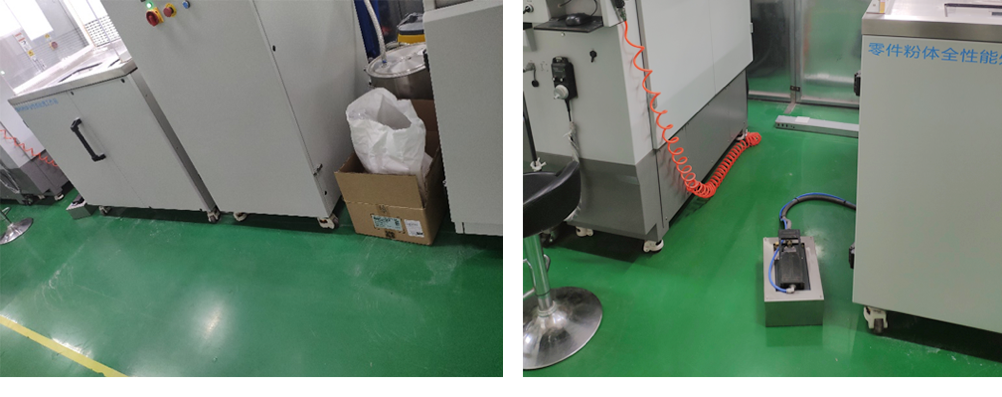
ren och städad miljö
5.Kostnadsminskning och effektivitetsförbättring:
Innan SLS 3D-utskriftssystem introducerades antog kunden CNC-bearbetning eller outsourcad silikonbeläggningsbearbetning, vilket tog minst 5-6 dagar att erhålla testdelarna. Efter att lasersintringssystemet P360 sattes i produktion kunde prover erhållas och testas efter bara 48 timmar, vilket sparar tid med mer än 60%. Tidigare kostade outsourcad ärendehantering cirka 4 000 RMB / set. Med SLS 3D-utskriftsteknik kan kostnaden styras under RMB 700/set, en minskning med mer än 80%. Med en hög utnyttjandegrad kan kundens utrustning för närvarande skriva ut 2-3 hela kammaren per vecka i genomsnitt. Dessutom kan det enligt kunden spara cirka 700 000 RMB per år, vilket bättre minskar kostnaderna och förbättrar effektiviteten.
Jämförelse av kostnad och cykel mellan traditionell process och SLS 3D-utskriftsprocess:
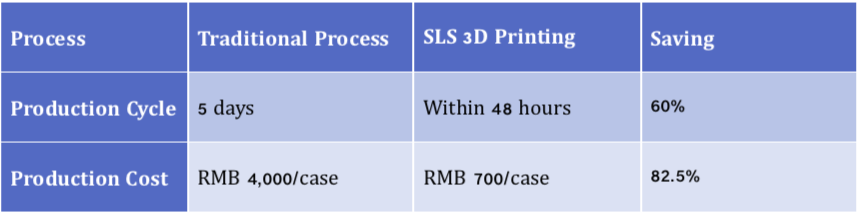
"TPM3D: s P360-system är bekvämt och snabbt; PPS minskar manuell intervention samtidigt som man uppnår hög bearbetningseffektivitet för delar och pulver. Lösningen sparar tid och kostnader och säkerställer en snygg och säkrare miljö."
——Feedback från kunden